Definition and Principles of Solvent-Free Lamination
After analyzing the dry cured process, let’s explore the solvent-free composite. The biggest differences between solvent-free and dry-cured processes lie in two aspects:
- Adhesive Application: The change in adhesive brings about a change in the application method.
- Absence of Organic Solvents: The adhesive does not contain organic solvents, so it no longer needs to be heated in a drying oven.
To achieve a more uniform coating and gluing effect, solvent-free composites usually adopt a five-roll coating and gluing method.
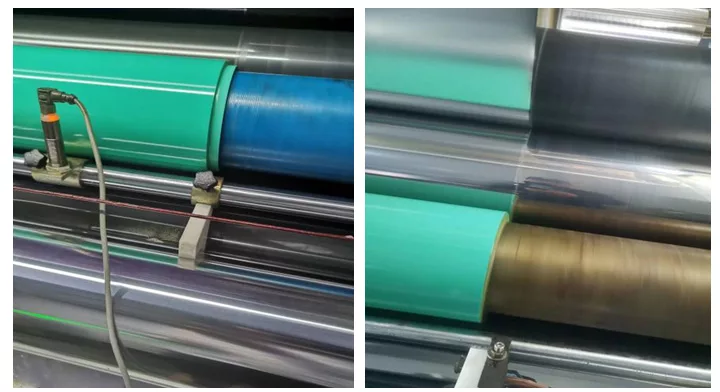
Cost and Environmental Benefits
Due to the change in coating method, the amount of glue applied during lamination can be reduced, and the solid content of the glue can reach 100% without volatile organic solvents. Therefore, solvent-free lamination brings significant cost advantages to flexible packaging. The process of eliminating solvent drying not only significantly saves energy consumption in production but also solves the problem of VOCs treatment at the composite end.
Advantages of Solvent-Free Solutions
Solvent-free solutions have solved many issues in the production of flexible packaging, such as cost, efficiency, energy, and environmental protection. They offer sustainable development solutions for plastic flexible packaging and have greatly improved and expanded the possibilities of composite methods. As a result, the solvent-free approach has rapidly developed and become popular in the composite flexible packaging industry over the past decade.
Changes in Adhesives, Coating Methods, and Equipment
Solvent-free composite brings significant changes in adhesives, coating methods, equipment requirements, and operational skills. Compared with dry composite, each method has its own advantages and disadvantages, with corresponding applications in different fields.
Adhesive Properties
- Solvent-Free Adhesives: These adhesives do not contain organic solvents and theoretically can use adhesives with 100% solid content. To apply more efficiently and stably, traditional wire rollers cannot be used for adhesive transfer.
- Roller Coating Transfer: Most equipment currently adopts this method for adhesive application, which requires relatively high technical operation and adhesive requirements. Construction must be carried out under strict process conditions to increase the stability of the coating.
Stability in Solvent-Free Lamination
There are four key aspects of stability in solvent-free lamination:
- Adhesive Stability: The stability of the adhesive itself.
- Coating Stability: The stability of the adhesive coating state.
- Equipment Reliability: The stability and reliability of the equipment.
- Adhesion Integrity: The need for strong and reliable adhesion after coating is completed.
Five-Roll Coating Method
The solvent-free coating method adopts a five-roll coating system. This involves transferring the adhesive onto the composite steel roller through the gap between the measuring roller and the transfer steel roller, then bonding it through the composite rubber roller. The change in the adhesive coating method allows for a more even application to the film. Typically, a coating amount of 1-2 g/㎡ can achieve good composite effects, with a significant decrease (40%-60%) compared to dry coating. The thinning of the coating layer also reduces the cohesive force of the adhesive shrinkage.
High-Speed Coating and Adhesive Viscosity
To achieve a stable coating effect in high-speed compounding, in addition to ensuring equipment accuracy and stability, the adhesive also needs a stable working viscosity. The working viscosity of common adhesives is mostly between 800-1500 CPS (about 22-36S for 4 cups), and the working temperature is in the range of 35-50°C.
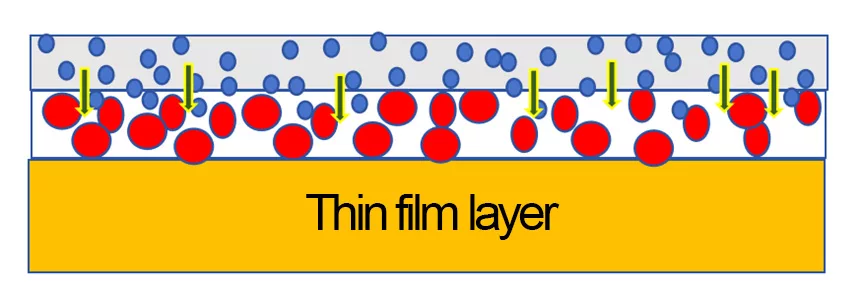
Managing Viscosity
This working viscosity is relatively low for glue. To maintain good working viscosity, two methods can be used:
- Reducing Initial Viscosity: Lowering the molecular weight of the original adhesive, which may lower the initial adhesion force.
- Increasing Adhesive Viscosity with Temperature: Raising the construction temperature to reduce viscosity, though this may increase the reaction rate and shorten the adhesive’s constant viscosity time.
Following the inertia thinking of adhesive research and development, by controlling the molecular weight (initial viscosity) of the original adhesive, the initial reaction rate is extended, simultaneously increasing the storage and coating performance of the adhesive. The formula design of glue must balance these contradictions.
Equipment Considerations
The solvent-free five-roll coating process uses heated steel rollers, while the middle transfer roller and composite pressure roller are glue rollers. The uniformity of heating and thermal deformation of the rubber roller during equipment coating can affect the normal performance of the coating.
Adhesive Mixing
The solvent-free working adhesive solution is mixed by a glue mixer. The glue ratio and uniformity of A/B glue must be accurate. Before each start-up, it’s crucial to inspect and confirm the glue output and mixing status to prevent abnormalities.
Differences Between Solvent-Free and Dry Coating
The biggest difference between solvent-free and dry coating is the absence of a drying process, eliminating the need for hot air and heating. This simplifies energy saving and equipment structure, significantly improving the speed of the laminating machine. With increased machine speed, higher stability requirements are placed on equipment tension, particularly due to the extremely low initial adhesion of the laminating.
Challenges in Solvent-Free High-Speed Composite
- Adhesive Selection: Low initial adhesion can cause misalignment.
- Precise Adhesive Application: Over-application may cause issues like ink dissolution; under-application may cause problems like white spots.
- Film Quality: Poor thickness and flatness can negatively impact lamination.
- Environmental Conditions: Maintaining constant temperature, humidity, and dust-free environments is crucial.
The variability of roll diameter in unwinding is greater, resulting in more significant stress changes on the film. Higher precision operation and standardization of the solvent-free production process are vital.
Curing Considerations
Solvent-free curing, especially the curing of the inner core in the roll, requires careful control of curing, stress changes in the film, interlayer creep, and electrostatic effects.
Conclusion
In summary, to achieve the best composite results, it’s essential to have a clear understanding of the principles of glue, film, equipment, and process. Properly matching and setting up processes in advance ensures the production of composite products that are “glued more firmly and better.”